- Submit an enquiry to a product.
- Wait for a call from nearest supplier from your area.
- Get quote and product details.
- Choose best from them.
Centrifugal Pumps for Power Supply
Minimax Pumps Private Limited from NashikWe have marked a distinct position in the market by providing an excellent range of Centrifugal Pump.
per Piece
Single Stage Centrifugal Pump
Ambica Machine Tools from AhmedabadWe are offering a wide range of Single Stage Centrifugal pump. Features: Quick delivery E.
per Piece
Cast Iron Industrial Centrifugal Pump
Creative Engineers from AhmedabadCast Iron Industrial Centrifugal Pump .
SS Milk Pumps
Ved Engineering from Greater NoidaOur reputation in the market is largely attributable to our best quality range of SS Centrifugal Pum.
Stainless Steel 316l/304 Sanipure Sanitary Centrifugal Pumps, SWSCP1HP, 30000lph
Sanipure Water Systems from MumbaiWe offers wide range of Sanitary Centrifugal Pumps for Pharma/ Pure Water/Dairy/ Food Industry. This.
per Piece
Self Priming Centrifugal Pump Set, 2900 & 1450 RPM
Tech-mech Engineering Co. from MumbaiOur clients can avail a quality range of Self Priming Centrifugal Pump Set from us. All these self-p.
per Piece
MS Single Phase Self Priming Centrifugal Pump, 110-230 V
VND Plastico Pumps Private Limited from VadodaraWe offer Self Priming Centrifugal Pump. It is a single stage horizontal centrifugal pump. Plastico P.
per No
2 hp Single Phase Centrifugal Water Pump
Unisoft Pheripherials from RajkotA centrifugal pump is a rotodynamic pump that uses a rotating impeller to increase the pressure and .
per Unit
Johnson Combinormm Centrifugal Pumps
Makharia Machineries Pvt. Ltd. from MumbaiThe CombiNorm is a centrifugal pump according to EN733 (DIN 24255). This is one of the most versatil.
Self Priming Centrifugal Jet Pumps
KSB Pumps Limited from PuneWe are offering Self Priming Centrifugal Jet Pumps to our clients. .
Self Priming Sanitary Centrifugal Pump
FEC India Private Limited from ChennaiPumps in the LKHSP series are self priming,which means they can be used to pump products containing .
per Piece
DC Centrifugal Pumps
Reliable Engineers from AhmedabadWith the valuable assistance of our skilled team of professionals, we have been able to come up with.
per Piece
Ci Single Phase Centrifugal End Suction Pump, Size: 32 To 200 Mm, Up To 3500 Rpm
Shivam Enterprise from AhmedabadCentrifugal End Suction pump with Open/Semi-Open Impeller We are noteworthy in this organization, en.
per Piece
Suction Centrifugal Pump
Mackwell Pumps & Controls from AhmedabadProduct Description: These pumps are apt for Chemical, Petrochemical Power generation application.
per Piece
Solvent Transfer Pump
Micro Tech Engineering from New Delhi• Head : 80 meter • Capacity &n.
per Set
Centrifugal Boiler Feed Pump
Pump Engineering Co. Private Limited from AhmedabadWe offer Centrifugal Boiler Feed Pump. It is a high pressure multistage pumps. It is accompanied wit.
per Piece
Hygienic Centrifugal Pumps
Alpha Neutech Pump & Systems from CoimbatoreBy keeping track of current market development, we are offering an excellent range of hygienic centr.
Prisma - Horizontal Multi-stage Centrifugal Pump
Aquatech Engineers from New DelhiQuiet-running multi-stage centrifugal pumps. Available with Pressure Kit. App.
Sanitary Centrifugal Pumps
All Flow Pumps & Engineers from HyderabadSanitary Centrifugal Pumps which are made using premium quality raw materials and modern machines an.
Self Priming V Type Centrifugal Pump
S. K. Das & Brothers from HowrahWith our years of experience, we are indulged in manufacturing Self Priming V type Centrifugal Pump..
S. S. Monoblock Centrifugal Pump with Trolley
S. R. Industries from NagothaneS. S. Monoblock Centrifugal Pump with Trolley .
High Speed Water Pump, Speed: up to 3500 RPM
Sujal Engineering from AhmedabadBy keeping track with the market development, we are offering optimum quality High Speed Water Pump .
per Number
Jee Pumps Up To 350 Mtrs Cast Iron Multi Stage Centrifugal Pump
Jee Pumps (Guj) Private Limited from AhmedabadWe offer Multi-Stage Centrifugal Pump. “JEE pumps” series JCBFP pumps are vertical split.
per Piece
Slurry Pumps, Max Flow Rate: 5 - 400 cube per hour
Creative Engineers from AhmedabadWe are the suppliers of Slurry Pumps.Applications:“PS” type pumps are used in paper & pu.
per Unit
1 hp Single Phase Centrifugal Pumps
DPL Valves & Systems Private Limited from MumbaiWe are a leading manufacturer and supplier of centrifugal pumps and lobe pumps for many pharmaceutic.
per Piece
Electric Centrifugal Monoblock Pump, Voltage: 110-415 V
Tech-mech Engineering Co. from Mumbai.
per Piece
Stainless Steel 316 Horizontal Centrifugal Pump, Speed: Up to 3500 RPM
VND Plastico Pumps Private Limited from VadodaraWe are providing Horizontal Centrifugal Pump Application: Hot and cold water circulati.
per No
Three Phase Centrifugal Self Priming Mud Pumps, Capacity: 250 m3/hr
SMS Pump & Engineers from AhmedabadBacked by our experienced team of professionals, we have been able to put forth a quality assured ar.
per No
Single Phase Metallic Centrifugal Pump, 240 V
Propeller Pumps from Ahmedabad.
per Piece
Single Stage TOSS Industrial Centrifugal Pump, Electric
Reliable Engineers from AhmedabadWith the valuable assistance of our skilled team of professionals, we have been able to come up with.
per Piece
Hamraj Electric Centrifugal Monoblock Pump, 380 V
Hamraj Enterprises from GhaziabadWe are leading supplier & distributor of Monoblock Centrifugal Pump. .
per Piece
JIKSAN Blue Gland/Mechanical Self Priming Bare Shaft Non-Clog Pumps, Electric, Capacity: Up To 650 M3/hr
Shivam Enterprise from AhmedabadOperating Range:Capacity: Up to 650 M3/hrHead: Up to 50 meterDischarge Size: Dn 40 to 200 mmTemperat.
per Piece
Khyati Single Stage Centrifugal Monoblock Pump, Model Name/Number: Kcm - 111
Khyati Enterprise from RajkotWe are successfully meeting the varied requirements of our clients by providing the best quality ran.
per Unit
Kirloskar Stainless Steel Electric Centrifugal Pumps, Warranty: 1 Year
Zed Plus Enterprise from Ahmedabad.
per Piece
Mackwell Cast Iron Centrifugal Process Pump
Mackwell Pumps & Controls from AhmedabadHot and cold water circulation cooling water circulationDrip irrigation water supply and building se.
per Piece
LEAKLESS Upto 150 Mtr Monoblock Centrifugal Pump, Max Flow Rate: Upto 250 M3/Hr, Model: LMP
Leakless (india) Engineering from MumbaiMonoblock Centrifugal Type Pumps Are Mainly Designed To Occupy Less Space As Compare To Coupled Pump.
per Number
BEHP CI or SS End Suction Centrifugal Pump, Horizontal
Beseem Solutions Private Limited from KolkataBeing the trusted industry in the market, we are involved in offering a wide assortment of End Sucti.
per Number
Globe Star Cast Iron Horizontal Centrifugal Pump, 0.5 HP, Electric
Globe Star Engineers (India) Private Limited from AhmedabadWe are instrumental in offering optimum quality Horizontal Centrifugal Pump, is made in-line with th.
per Number
Cast Iron Diesel Centrifugal Water Pump
Prabhukrupa Industrial Corporation from Rajkot.
per Piece
Electric Rubberlined Centrifugal Pump
Fluidotech Pumps & Equipment Private Limited from New Delhi.
per Unit
Everest Analyticals Horizontal Centrifugal Pump, Available, Maximum Discharge Flow (in LPM): Differs
Everest Analyticals from ThaneWe are a leading name in the manufacturing and exporting of Horizontal Centrifugal Pumps. .
per ONWORDS
End Suction Centrifugal Pumps
Mukund Enterprise from AhmedabadTo cater the variegated needs of our esteemed customers, we are highly engaged in offering a wide ar.
per Piece
End Suction Centrifugal Pump
Guru Teg Bahadur Engineering Works from SonipatWe are a unique name in the industry, devoted towards offering the best quality range of End Suction.
per Piece
Multistage Centrifugal Pump
SSR Engineering from CoimbatoreIn order to keep pace with never ending demands of the customers, our company is instrumental in off.
per Unit
Centrifugal Pump
Perfect Engineers from VadodaraPioneer in this industry, we are engaged in providing a high-quality range of Centrifugal Pump.Detai.
per Piece
Victor/ Stanflo Three Phase Semi Impeller Self Priming Water Pump
Standard Global Supply Pvt. Ltd. from PuneWe bring forth vast industrial experience and expertise in this business, involved in offering a hig.
per Piece
SS Centrifugal Monoblock Pump
Nipa Commercial Corporation from Navi MumbaiLow Voltage Centrifugal Monoblock Pumpsets Up To 25 H.p:Horizontal Openwell Pumpsets Up To 15 H.p.Ve.
per Piece
Centrifugal Process Pump
Bhagylaxmi Trading from AhmedabadWith sincerity and hard work of our professionals, we have carved a niche for ourselves in this doma.
per Piece
End Suction Centrifugal Pump
Shivpumps & Equipments from ValsadBeing one of the renowned firms in the industry, we are decidedly involved in providing a high-quali.
per Piece
Centrifugal Pumps
Pump Engineering Co. Private Limited from AhmedabadCentrifugal Pumps .
per Piece
Polypropylene Centrifugal Pump
Acme Engineering Industries from AhmedabadWe are a highly acclaimed name in offering the best range of Polypropylene Pumps. These are availabl.
per Unit
Centrifugal Process Pump
Deval Enterprise from AhmedabadOwing to our years of industry experience and precise knowledge of this domain, we are offering an o.
per Piece
PP Centrifugal Pump, Electric
Moni Pumps & Equipments from MohaliPP Centrifugal Pumpmajorely this is used for chemical plant and pharmaceticual plant and stell plant.
per Piece
Centrifugal Pumps, Electric
Skymech Engineers from JaipurTaking end suction pumps to a new level By combining high efficiency with high flexibility regarding.
per Piece
Polypropylene Centrifugal Pump
Shreya Engineering from ValsadBacked by years of industry experience, we are engaged in offering a premium quality range of P.
per Piece
Centrifugal Pump
Navkar Engineering from AhmedabadBeing one of the trusted firms in the industry, we are highly engaged in providing a unique range of.
per Piece
Self Priming Centrifugal Pump
Mahaveer Industry from CoimbatoreOwing to the rich industrial experience and expertise in this business, we are involved in providing.
per Piece
Horizontal Multistage Centrifugal Pump
Pumps Care Technology from CoimbatoreIn order to keep pace with the never-ending demands of customers, we are involved in offering a wide.
per Unit
Centrifugal Water Pumps
New Bombay Electricals & Hardware from PuneCentrifugal Water Pumps.
per Piece
Stainless Steel CNP Horizontal Multistage Pump
Flow Tech Systems from ChennaiLeveraging the skills of our qualified team of professionals, we are instrumental in offering a wide.
per Piece
Centrifugal Polypropylene Pump
Anuvintech Pumps & Systems from PuneWe are offering Centrifugal Polypropylene Pump to our clients. .
per Piece
8 hp Stainless Steel Three Phase Horizontal Centrifugal Pump
Harihar Enterprises from DelhiWe have marked a distinct position in the market by providing an excellent range of Horizontal Centr.
per Unit
Single Phase Multi Stage Centrifugal Pumps for Agricultural, Motor Horsepower: 5 hp
Ceto Water from PuneMulti Stage Centrifugal Pumps.
per Piece
Horizontal Single Stage Pumps
Sedan Engineering Enterprises from HyderabadEngineered with utmost precision and perfection, the range of our Horizontal Single Stage Pumps find.
per Piece
Investment Casting SS Pumps
Hmp Pumps & Engineering Private Limited from Chennai.
per No
0.5 HP Single Phase Centrifugal Regenerative Pump, Max Flow Rate: 700 Lpm, Model Name/Number: Neon-NH60
Sagar Electric And Hardware Stores from Mumbai.
per Unit
Two Stage Cast Iron Three Phase Centrifugal Monoblock Pump
M/s Dinesh Agency from Indore.
per Piece
UNIFORCE Single Stage Titanium Centrifugal Pumps, Water Cooled
Uniforce Engineers from Chennai.
per Piece
Cast Iron 2 HP Cast-iron Single Stage Centrifugal Pump
Hindustan Engineering And Company from Chennai.
per Piece
CNP Single Stage RO Feed Pump, Electric, Air Cooled
H 2 O Ion Exchange from Ahmedabad.
per Unit
KSB Multi-Stage Centrifugal Pump, For Industrial
Eminent Engineering Services from Kolkata.
per Piece
Single Stage 2 HP Regenerative Centrifugal Pump, 2900 Rpm, Air Cooled
Raja Industrials from Chennai.
per Unit
114 M Stainless Steel CNP CDL 4-12 SS 304 Centrifugal Pump
Pervel Water Management Solutions from Chennai.
per Number
Single Phase Polypropylene Centrifugal Pump, Maximum Flow Rate: 2900 RPM
Jetro Sales from Jamshedpur.
per Piece
Three Phase Ebara Pumps Horizontal Centrifugal Pump
Oms Hydraulics from Mumbai.
per Unit
Kirloskar Centrifugal Pump
Delta Pumps & Heat Transfer Systems from New Delhi.
per Number
Liquid Transfer Pump (Centrifugal Type)
Reva Pharma Machinery from Vadodara.
per Unit
Sameer Cast Iron Self Priming Water Pump, 1700 rpm
Corsa Pump Agencies from Secunderabad.
per Unit
Centrifugal Pumps Price List in India
Product Name | Price in INR | City |
---|---|---|
High Speed Water Pump, Speed: up to 3500 RPM | 6900.00 / Number | Ahmedabad |
Jee Pumps Up To 350 Mtrs Cast Iron Multi Stage Centrifugal Pump | 22000.00 / Piece | Ahmedabad |
Slurry Pumps, Max Flow Rate: 5 - 400 cube per hour | 40000.00 / Unit | Ahmedabad |
1 hp Single Phase Centrifugal Pumps | 15000.00 / Piece | Mumbai |
Electric Centrifugal Monoblock Pump, Voltage: 110-415 V | 13000.00 / Piece | Mumbai |
Stainless Steel 316 Horizontal Centrifugal Pump, Speed: Up to 3500 RPM | 9990.00 / No | Vadodara |
Three Phase Centrifugal Self Priming Mud Pumps, Capacity: 250 m3/hr | 18000.00 / No | Ahmedabad |
Single Phase Metallic Centrifugal Pump, 240 V | 20000.00 / Piece | Ahmedabad |
Single Stage TOSS Industrial Centrifugal Pump, Electric | 18000.00 / Piece | Ahmedabad |
Centrifugal Pumps Brands List
-
Centrifugal Pumps
-
Kirloskar Centrifugal Pumps
-
CRI Centrifugal Pumps
-
Crompton Centrifugal Pumps
-
Texmo Centrifugal Pumps
-
KSB Centrifugal Pumps
-
Havells Centrifugal Pumps
-
Oswal Centrifugal Pumps
-
Apex Centrifugal Pumps
-
V-Guard Centrifugal Pumps
-
Usha Centrifugal Pumps
-
Suguna Centrifugal Pumps
-
Grundfos Centrifugal Pumps
-
Beacon Centrifugal Pumps
-
Centrifugal Pumps
-
Jain Centrifugal Pumps
-
Varuna Centrifugal Pumps
-
Topland Centrifugal Pumps
-
Sileaf Technologies Pvt. Ltd. Centrifugal Pumps
-
RK Centrifugal Pumps
-
Sujal Centrifugal Pumps
-
hindustan Centrifugal Pumps
Top 10 Centrifugal Pumps Manufacturers / Suppliers List in India
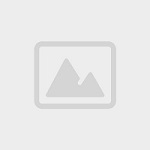
Makharia Machineries Pvt. Ltd.
From Mumbai, Maharashtra, India, 400025
Makharia Machineries Pvt. Ltd. is suppliers from Mumbai. It is established in year 1968 and having 400 plus employees.The contact address of Makharia Machineries Pvt. Ltd. is No. 310/311, Nav Neelam Building Dr. R. G. Thadani Marg, Worli.
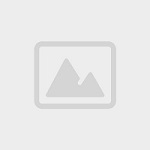
SMS Pump & Engineers
From Ahmedabad, Gujarat, India, 382445
SMS Pump & Engineers is suppliers from Ahmedabad. It is established in year 2010 and having 200 plus employees.The contact address of SMS Pump & Engineers is 195, Pushpak Industrial Estate, Old Nika Tube Compound Phase I, GIDC, Vatva.
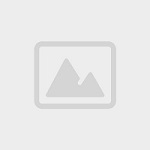
Mach Power Point Pumps India Private Limited
From Kolkata, West Bengal, India, 700001
Mach Power Point Pumps India Private Limited is suppliers from Kolkata. It is established in year 2004 and having 100 plus employees.The contact address of Mach Power Point Pumps India Private Limited is No. 21/A, Canning Street, Ground Floor.
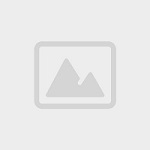
Laxmi Enterprises
From Gurgaon, Haryana, India, 122002
Laxmi Enterprises is suppliers from Gurgaon. It is established in year 2001 and having 100 plus employees.The contact address of Laxmi Enterprises is BM Plaza, Office No. 17, Krishna Market.
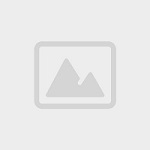
Shri Jagdhamba Enterprises
From Hyderabad, Telangana, India, 500003
Shri Jagdhamba Enterprises is suppliers from Hyderabad. It is established in year 2002 and having 100 plus employees.The contact address of Shri Jagdhamba Enterprises is No. 3-A, 3rd Floor, Maitri Arcade.
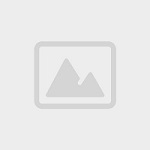
Anmol Pharma Equipments
From Nagothane, Maharashtra, India, 400604
Anmol Pharma Equipments is suppliers from Nagothane. It is established in year 2002 and having 100 plus employees.The contact address of Anmol Pharma Equipments is C/o Shahani & Sons Industries, Plot No. A-437, Lane No. 3, Road No. 28 Opposite Emco Co., Gate No. 3, Wagle Estate.
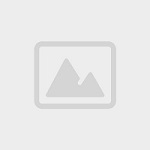
Jaya Industries, Kolkatta
From Kolkata, West Bengal, India, 700028
Jaya Industries, Kolkatta is suppliers from Kolkata. It is established in year 1969 and having 300 plus employees.The contact address of Jaya Industries, Kolkatta is No. 543, Jessore Road Dum Dum.
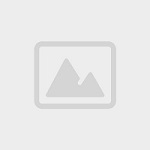
Parshwa Traders
From Mumbai, Maharashtra, India, 400003
Parshwa Traders is suppliers from Mumbai. It is established in year 1992 and having 100 plus employees.The contact address of Parshwa Traders is 34, Nagdevi Street 212, Karani Niwas.
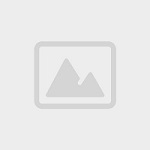
Ken Engineers
From Ahmedabad, Gujarat, India, 380027
Ken Engineers is suppliers from Ahmedabad. It is established in year 2000 and having 100 plus employees.The contact address of Ken Engineers is No. 309, Nandanvan Complex, Opposite RTO, Subhas Bridge Circle.
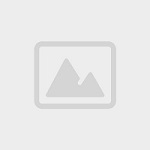
Jain Electricals
From Kolkata, West Bengal, India, 700001
Jain Electricals is suppliers from Kolkata. It is established in year 1977 and having 100 plus employees.The contact address of Jain Electricals is No. 21A, BRB Basu Road Near Canning Street.
Frequently Asked Questions on Centrifugal Pumps
1. What are centrifugal pumps
Centrifugal pumps are used to transport fluids by the conversion of rotational kinetic energy to the hydrodynamic energy of the fluid flow.
2. What are different types of Centrifugal pump
There are two types of centrifugal pumps that are mostly used centrifugal pumps that are useful for transferring fuel and other types of liquid and including radial and axial centrifugal pumps.
Radial centrifugal pumps smooth a flow that is sped up in an outward moving via a pump the rotating part of a centrifugal pump, compressor, or other machine designed to move fluid by rotation.
3. What are some features of Centrifugal pumps
- The centrifugal pumps impart momentum to the fluid by rotating impellers that are immersed in the fluid.
- The momentum produces an increase in pressure or flow at the pump outlet.
- Centrifugal Pumps come in many different shapes and sizes.
- The Centrifugal pump is a long term asset and free from regular maintenance.
- Centrifugal Pumps have been designed with fewer parts to troubleshoot and maintain pumps quickly and efficiently
4. Centrifugal pumps used for
The Centrifugal pumps are used to transport fluids by the transformation of rotational kinetic energy to the hydrodynamic energy of the fluid flow. The rotational energy typically comes from an engine or electric motor. They are a sub-class of dynamic axisymmetric work-absorbing turbomachinery.
5. What is the some advantage of centrifugal pump?
Advantages of the centrifugal pump such as their aforementioned simplicity.
- It also allows them to move at high speeds with minimal maintenance
- This makes it easy to produce with many different materials.
- They don't require any valves or many moving parts.
6. What are the limitations of a centrifugal pump
The efficient operation of a centrifugal pump relies on the constant, high-speed rotation of its impeller. With high viscosity feeds, centrifugal pumps become increasingly inefficient: there is greater resistance and higher pressure is needed to maintain a specific flow rate.
7. What are the Common parts of centrifugal pump?
The Common parts of the centrifugal pump found in centrifugal pumps are Pump main housing, bearings, Motor, Coupling, Shaft-drive, Impeller, sealImpeller, Shaft seal.
8. What is the difference between the centrifugal pump and other rotational pumps
The difference between centrifugal and other rotational pumps is that the centrifugal pump is one of the rotary pumps which used the kinetic energy of the impeller. another rotational pump is a positive displacement type pump which is forced by a piston.
9. Which types of motor are used in the centrifugal pump
The centrifugal pumps are the used induction motor Most of the centrifugal pumps are powered by an induction motor. A squirrel cage induction motor is used in a water pump that comes with a 3 phase AC supply. Such motors are less efficient as they are standardized and not individually designed for specific applications.
10. What are centrifugal pumps made of
Centrifugal pumps contain a set of rotating vanes called an impeller. The rotary vanes are usually.
encircle within a housing or casing, and are used to impart energy to a fluid through centrifugal force.
Types of Centrifugal pumps
Centrifugal pumps are of several types depending on the number of impellers, design, construction, service, and many more. Here, we describe all the types based on several factors:
Based on the number of impellers, Centrifugal pumps are of three types:
- Single stage: In this type, one impeller is present which means it has a simple design and easy to maintain.
- Two-stage: Two impellers are present which operate side by side, used for medium head applications.
- Multi-stage: Used for high head application, this type includes three or more impellers.
On the basis of a type of impeller:
- Single Suction: It has one suction in impeller which means fluid enters in blades through only one side. Although its design is simple, it has one limitation which is impeller imbalance due to flow coming in one side.
- Double suction: It overcomes the limitation of impeller imbalance because it is double suction impeller which means fluid enters from both sides of blades.
On the basis of shaft orientation:
- Horizontal: In these pumps, the shaft is in the horizontal plane. It is popular because of easy to maintain and service.
- Vertical: In these pumps, a shaft is in the vertical plane. They require large headroom for maintenance, installation, and service.
Depending on the compliance with industry standards:
- ANSI pump: It stands for American National Standards Institute that refers to dimensional standards. The standards ANSI B73.1 and ASME B73.1 must meet by the pumps.
- API pump: American Petroleum Institute refers to the parameters of pump’s constructions. The pump must meet the requirements of API standards 610 for General Refinery Service.
- ISO pumps: Those pumps that come under ISO pumps must follow ISO 2858, 5199 specifications.
- Nuclear Pumps: The pumps follow ASME specifications.
- DIN pump: Pumps have DIN 24256 specifications, used in large flow rates, very high temperatures, or high working pressures.
On the basis of case-split:
- Axial split: In these, the volute casing splits axially and the split line is at the center line of the shaft. They are mounted horizontally because of easy to maintain and install.
- Radial split: In this, the volute casing splits radially which means the split line is perpendicular to shaft center line.
Components of Centrifugal pumps:
The components are divided mainly into two primary classes that are a wet end and the mechanical end. The wet end of the pump has those parts that determine the hydraulic performance whereas the mechanical end has those parts that help impeller to rotate within a casing. The wet end includes impeller, casing, and mechanical end includes a shaft, shaft sealing, bearings, pipes, etc.
- Impeller: It is the most important component of centrifugal pumps. It is the rotating part of the system which is used to increase the speed of flow. It is mounted on the shaft which is connected with a motor that is used to rotate the impeller.
- Casing: It surrounds the impeller with an airtight passage and acts as a pressure containment vessel. The main work of casing is to provide the flow of liquid in and out of a centrifugal pump. Generally, three types of the casing are used: volute casing, vortex casing, and casing with Guide blades.
- Shaft sealing: It is the special part of centrifugal pumps as it is used to prevent the leakage of the fluid.
- Bearings: It is used to reduce the friction between the shaft and the stator.
- Suction pipe: It is the pipe whose one end is in the water sump and another part is connected with an inlet of an impeller. At the end of the suction pipe, strainer and foot valve are connected. A strainer is used to filter the water and block the unwanted particles.
- Delivery Pipe: It is the pipe whose one end is in the tank where water has to deliver and one end is connected with an outlet of the pump.
Applications of centrifugal pumps:
It is true that a centrifugal pump is the most demanding choice for fluid movement which makes it useful in many industries. Here, we present some applications of centrifugal pumps:
- Dairy Industry: Centrifugal pumps are used to transfer liquid products such as milk, buttermilk, etc.
- Agriculture and Manufacturing: Used for drainage, wastewater processing plants, irrigation and many more.
- Oil & energy: Pumps are used for movement of crude oil, mud, refinery plants, etc.
- Pharma and Cosmetic Industry: Here, pumps are used to transfer glucose, lactose and other chemical substances.
Advantages of centrifugal pumps
The centrifugal pumps are the popular choice for the movement of fluids for below reasons. Get a look at them:
- The utmost advantage of a centrifugal pump is its simplicity. It is small in size and doesn't have complex parts to maintain. This means they need less space to install.
- They are not expensive which means they have a lower capital cost and easily affordable.
- The output of centrifugal water pumps is steady and uniform.
- They can handle any type of fluids which means handle with low to high viscous fluids.
- They are easily maintainable and can be cleaned very quickly.
- They can handle with corrosive and edible types of fluids.
- They are leek free that ensures safety from the toxic fluids.
Disadvantages of centrifugal pumps:
Although, centrifugal pumps are great in use but still, they have some disadvantages which are:
- The main disadvantage is that they use rotation instead of suction which means they have to be underwater to move water.
- They can’t give optimal output with high viscous fluids.
- The size of pumps is also restrictable.
- They don’t produce high pressure as per requirement.
Explore By Cities
- Centrifugal Pumps in Nashik
- Centrifugal Pumps in Ahmedabad
- Centrifugal Pumps in Greater Noida
- Centrifugal Pumps in Mumbai
- Centrifugal Pumps in Vadodara
- Centrifugal Pumps in Rajkot
- Centrifugal Pumps in Pune
- Centrifugal Pumps in Chennai
- Centrifugal Pumps in New Delhi
- Centrifugal Pumps in Coimbatore
- Centrifugal Pumps in Hyderabad
- Centrifugal Pumps in Howrah
- Centrifugal Pumps in Nagothane
- Centrifugal Pumps in Ghaziabad
- Centrifugal Pumps in Kolkata
- Centrifugal Pumps in Delhi
- Centrifugal Pumps in Thane
- Centrifugal Pumps in Sonipat
- Centrifugal Pumps in Navi Mumbai
- Centrifugal Pumps in Valsad
- Centrifugal Pumps in Mohali
- Centrifugal Pumps in Jaipur
- Centrifugal Pumps in Indore
- Centrifugal Pumps in Morbi
- Centrifugal Pumps in Jamshedpur
- Centrifugal Pumps in Bengaluru
- Centrifugal Pumps in Madurai
- Centrifugal Pumps in Secunderabad