- Submit an enquiry to a product.
- Wait for a call from nearest supplier from your area.
- Get quote and product details.
- Choose best from them.
Vacuum Pump
Servo Enterprisess from ChennaiVacuum Pressure Pumps are manufactured using premium grade raw material, which is sourced from trust.
per Unit
Liquid Ring Vacuum Pump
Leelam Industries from AhmedabadHere is the best liquid ring vacuum pump design, liquid ring vacuum pump manufacturer & who.
per Unit
Rotary Vane Oil Free Vacuum Pumps VT 4.4
Shiv Technology from PuneSimplicity of design with only one shaft and direct drive produces robust, long-lasting vacuum pumps.
per Unit
Oil Free Diaphragm Type Vacuum Pump
PCI Analytics Private Limited from MumbaiSalient Features:- • No Lubrication required • Absolutely Portable • T.
per Starting Per Piece
Vacuum Pump Oil
Dicon Products Private Limited from DelhiWe are offering Vacuum Pump Oil to our clients. best Vacuum pump price in your city. .
Everest Cast Iron Oil Sealed Rotary High Vacuum Pumps, Electric, 1500 Rpm
Everest Pumps & Systems from ThaneThese are of oil-immersed, rotary vane type pumps. There in-built non-return valve which prevents ba.
per Unit
Edwards rv12 Pump
Mackwell Pumps & Controls from MumbaiWe offer a wide range of Edwards rv12 Pump .
High Vacuum Pump
Proton Engineering Works from Mumbai‘PROVAK’ High Vacuum Pumps are manufactured in out well equipped factory, where our most.
Three Phase Diaphragm Vacuum Pump
Faco Automation from MumbaiWe are offering a wide range of Diaphragm Vacuum Pump. Model no VPD 25P MAX FLOW:25 ltrs/min.
per Piece
Liquid Ring Vacuum Pump
Anitha Engineers from HyderabadLiquid Ring Vacuum Pump Owing to our in-depth knowledge in this domain, we are specialized in p.
per Piece
Monoblock Vacuum Pump
Shri Saikrupa Engineering Works from NagothaneWe commence our business as the leading organization of the best quality Monoblock Vacuum Pump. .
1 HP Rotary Vacuum Pumps
Parikh Sales from Ahmedabad1 HP Rotary Vacuum Pumps We offer high-quality rotary vacuum pumps These types of units are use.
per Unit
Rotary Vane Pumps
Moscow Engineering Works from KanpurRotary vane pumps (fixed and simple adjustable displacement) have higher efficiencies than gear pump.
Liquid Ring Vacuum Pumps
Sawant High Vac Industries from MumbaiCustomers are provided with an optimum quality array of Liquid Ring Vacuum Pumps at market leading p.
Lab Vacuum Pump
Crozair Technicea from MumbaiHighly efficient in working, these Lab Vacuum Pump are best in quality and easier to use. Best for i.
Single Phase Double Stage Vacuum Pump
Vijay Trading Company from SuratSingle Phase Double Stage Vacuum Pump .
per Piece
Oil Sealed Rotary High Vacuum Pumps
RD Enterprises from FaridabadReckoned as one of the emergent companies of the industry, we are extremely immersed in providing of.
per Piece
Vacuum Pump
Gayathri Pumps from CoimbatoreBy keeping the track of latest market trend, we are highly efficient in manufacturing and supplying .
Single Stage Water Vacuum Pumps
Unique Vacuum Technology from AhmedabadWe are one of the leading manufacturer as well as supplier of Single Stage Water Vacuum Pumps. .
Rotary High Vacuum Pump
Shreeji Engineering from AhmedabadWe are engaged in manufacturing and supplying Rotary High Vacuum Pump. Features: Light in w.
per No
Direct Driven High Vacuum Pumps
Sabar Pumps Pvt. Ltd from AhmedabadDirect Driven High Vacuum Pumps We offer a variety of designs and shapes. we are actively.
per Piece
Diaphragm Vacuum Pumps
Ascent Engineers from HyderabadWith the help of our expert team members, we have been able to offer a wide range of Diaphragm Vacuu.
Diaphragm Vacuum Pumps
Sunshine Instruments from CoimbatoreWe are one of the renowned Exporter and suppliers of a wide range of Vacuum Pumps. A Vacuum Pump eje.
SAGA Double Stage Parag High Vacuum Pump, For Industrial
SAGA ENGINEERING CO from Ahmedabad.
per No
Automatic Single Stage Oil Seal Diaphragm Vacuum Pump
Maxima Resource from Bengaluru.
per Number
Single stage Direct Drive Rotary Vane Pumps Vacuum Pumps, 5
Alpha Vacuum Technology from Ahmedabad.
per Piece
Diaphragm Vacuum Pump
Innovative Engineering & Servicing from AhmedabadA diaphragm pump is a positive displacement pump that uses a combination of the recip.
per Piece
Diaphragm Vacuum Pumps
D K Sales Corporation from PuneAvail from us high quality, Diaphragm Vacuum Pumps, which are appreciated for enhanced performance. .
Oil Seal High Vacuum Pump
Whirler Centrifugals Private Limited from AhmedabadOil Seal High Vacuum Pump Proffered collection is massively appreciated fo.
per Piece
Vacuum Pumps
Coburg Equipments Pvt Ltd from BengaluruCOBCAT’s range of vacuum pump COBVAC series is the simple choice of demanding applications lik.
Vacuum Pump
National Constructions & Machinery from GhaziabadWe manufacture Vacuum Pumps that are oil-immersed, rotary vane type pumps. Featured with high-effici.
per Unit
Diaphragm Vacuum Pumps
Athena Technology from MumbaiDiaphragm Vacuum Pumps: We offer 100% oil-free Diaphragm Vacuum Pumps/Compressors. They can be used.
Shenovac Double Stage Vacuum Pump With Tank, Model Name/Number: Sv-5 Hvs, 2 Hp
.
per Number
Micronvac Engineers Single Phase Crompton Motor Vacuum Pump, Max Flow Rate: 30 Lpm
.
per Piece
Rotary Vane Vacuum Pump
Sai Hi Vac Enterprises from GhaziabadBeing a customer focused organization, we are engaged in offering a wide array of Rotary Vane Vacuum.
per Piece
Vacuum Pumping Systems
Flyvacuum Technologies Pvt. Ltd. from BengaluruVacuum pumping systems as per Requirement. Rough Vaccum / High Vacuum / Ultra High Vacuum. .
per Unit
Two Stage Rotary Vacuum Pump
INDIA VACUUM TECHNOLOGY from BengaluruDue to our enormous understanding and massive knowledge of this business, we are involved in offerin.
per Piece
Real Single Stage High Vacuum Pumps, Model Name/Number: 12VT
Real (A Brand of Talsania Engineering Works ) from AhmedabadHigh Vacuum Pumps Manufacturer & Exporter of Dry Vacuum Pump & Single & Two Stage Dry Va.
per Unit
Yash ACME-63 High Vacuum Pumps, For Industrial, 3 Hp
Yash Blowers Private Limited from FaridabadWe are renowned manufacturers of a comprehensive array of High Vacuum Pumps. Our products are highly.
per Piece
Vacuum Pump - Close Loop Seal Water Package
Meekaj Techno App Services from AhmedabadWe are an applauded name busy in offering for our valuable clients a superior quality range of Vacuu.
per Piece
Vacuum Pumps
Refrigeration Spare Centre from MumbaiWe are a Leading Supplier of all types of Vacuum Pumps. .
per Piece
Electric Vacuum Dewatering Pump
Maa Ambe Enterprises from New DelhiElectric Vacuum Dewatering Pump.
per Piece
Vacuum Pump
Scientific & Technological Equipment Corporation from New DelhiVacuum Pump are used for specific gravity test by removing air voids from the Bitumen Mix. Very usef.
per Piece
Jurop Vacuum Pump
Whale Enterprise Private Limited from CoimbatoreTo gain a strong foothold in this industry, we are devoted to offering a wide gamut of Vacuum Suctio.
per Piece
Carbon Vacuum Pumps, 220 V, 2hp (1.5kw),3hp
RD Enterprises from FaridabadOur company holds immense experience in this domain and is involved in presenting an enormous qualit.
per Piece
Vacuum Suction Pump
Super Tech Engineers from GhaziabadBeing one of the renowned firms in the industry, we are decidedly involved in providing a high-quali.
per Piece
Value Vacuum Pump AC Gas Charging, 220
Envico Instruments from New DelhiValue vacuum Pump manufacture by chinese Company we have been sale of these vacuum pump in many year.
per Piece
Max 10 Hp Dry Vacuum Pump, Capacity: Max 160 Metre Cube Per Hour
Sungrace Electro Systems from VadodaraRange: Vacuum up to 650mm (26”) of Mercury Air Flow Rate up to 55 m³/hr (242 USgp.
per Piece
Single Stage Vacuum Pump, Power: 110 V AC
Labline Stock Centre from MumbaiWe are manufacturer and trader of a quality range of Vacuum Pump that is sure to match the expe.
per Piece
Vacuum Pumps
BIBUS India Pvt Ltd from BengaluruCOAX® technology Piab's patent technology platform is an offshoot of the multistage technolo.
per Piece
Mastercool 90070 10- CFM Vacuum Pump
Infinity HVAC Spares & Tools Private Limited from MumbaiFeatures :Durable and time tested.Stands up to the the most gruelling conditions and provide years o.
per Piece
Mastercool Rotary Vane Deep Vacuum Pumps
Frigtools Refrigeration & Engineering Company from New DelhiOffering Rotary Vane Deep Vacuum Pumps. We also offer refrigerant recovery and recycling unit & infr.
per Piece
Vacuum Pump
Chilltech Engineers from AhmedabadHigh Vacuum pump for specially Vapour Absorption Chiller .
per Number
Direct Driven High Vacuum Pump
Creative Engineers from PuneHeavy duty high vacuum pump, it is very compact & noise less - the ultimate vacuum 0. 001mmhg wi.
per Number
DV Vacuum Pump
Spot India Group from Navi MumbaiSPOT INDIA GROUP IS LEADING SUPPLIER AND EXPORTER FORDV/Vacuum Pump .
per Unit
QEE Vacuum Pump, Warranty: 6 Months
Quality Enviro Engineers Private Limited from GhaziabadVacuum Pump (Exhauster/Compressor) The Rotary Sliding Vane, positive displacement type Exhauster/.
per Piece
Vacuum Pump
PCI Analytics Private Limited from MumbaiModel Max Flow (Ltrs/min) Max. VACCUM (inches / m.
per Starting Per Piece
Diaphragm Vacuum Pumps Single stage Vacuum Pump
Purple Ink from AmbalaWe manufacture high-end vacuum pumps that are durable and rugged. Our superior technology and materi.
per Piece
Industrial Vacuum Pumps
We arrange the best Industrial Vacuum Pump ranges & latest price list. Oper.
per Piece
10HP Vacuum Pump
We have provided a 10HP Vacuum Pumps. for latest price in India .
per Unit
Single Stage Vacuum Pump for Packaging
Quality House Keeping Material Supplier from Pune.
per Piece
Vacuum Pumps Price List in India
Product Name | Price in INR | City |
---|---|---|
Vacuum Pumps for Textile Industry | 15000.00 / Unit | Ahmedabad |
Single Stage Becker Make Vacuum Pump D250 | 110000.00 / Unit | Pune |
SAGA Double Stage Parag High Vacuum Pump, For Industrial | 1000.00 / No | Ahmedabad |
Automatic Single Stage Oil Seal Diaphragm Vacuum Pump | 30000.00 / Number | Bengaluru |
Single stage Direct Drive Rotary Vane Pumps Vacuum Pumps, 5 | 15000.00 / Piece | Ahmedabad |
Diaphragm Vacuum Pump | 10000.00 / Piece | Ahmedabad |
Oil Seal High Vacuum Pump | 25000.00 / Piece | Ahmedabad |
Vacuum Pump | 10000.00 / Unit | Ghaziabad |
Shenovac Double Stage Vacuum Pump With Tank, Model Name/Number: Sv-5 Hvs, 2 Hp | 125000.00 / Number | Delhi |
Vacuum Pumps Brands List
Top 10 Vacuum Pumps Manufacturers / Suppliers List in India
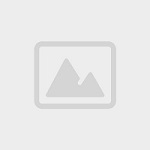
Akshat Enterprise
From Surat, Gujarat, India, 395003
Akshat Enterprise is suppliers from Surat. It is established in year 2009 and having 100 plus employees.The contact address of Akshat Enterprise is Capital Cinema, Delhi Gate, Main Road Dangi Sheri No. 3, Station Road.
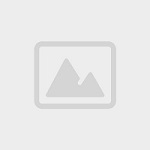
Servo Enterprisess
From Chennai, Tamil Nadu, India, 600096
Servo Enterprisess is suppliers from Chennai. It is established in year 1992 and having 300 plus employees.The contact address of Servo Enterprisess is 216, Burma Colony, Perungudi.
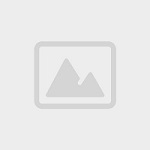
Yash Blowers Private Limited
From Faridabad, Haryana, India, 121001
Yash Blowers Private Limited is suppliers from Faridabad. It is established in year 2002 and having 200 plus employees.The contact address of Yash Blowers Private Limited is Unit 1 - PLOT NO- 4 NEAR 17 NO. CHUNGI NIT, Sector 49, Faridabad, Haryana India 121001 Unit 2 : Block No 861, Sector 69, IMT Faridabad.
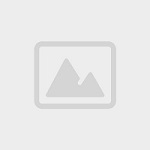
Creative Engineers
From Ahmedabad, Gujarat, India, 380028
Creative Engineers is suppliers from Ahmedabad. It is established in year 2002 and having 200 plus employees.The contact address of Creative Engineers is 4317, BEHIND TECHNO INDUSTRIES, PHASE-4, FOR U ROAD VATVA GIDC.
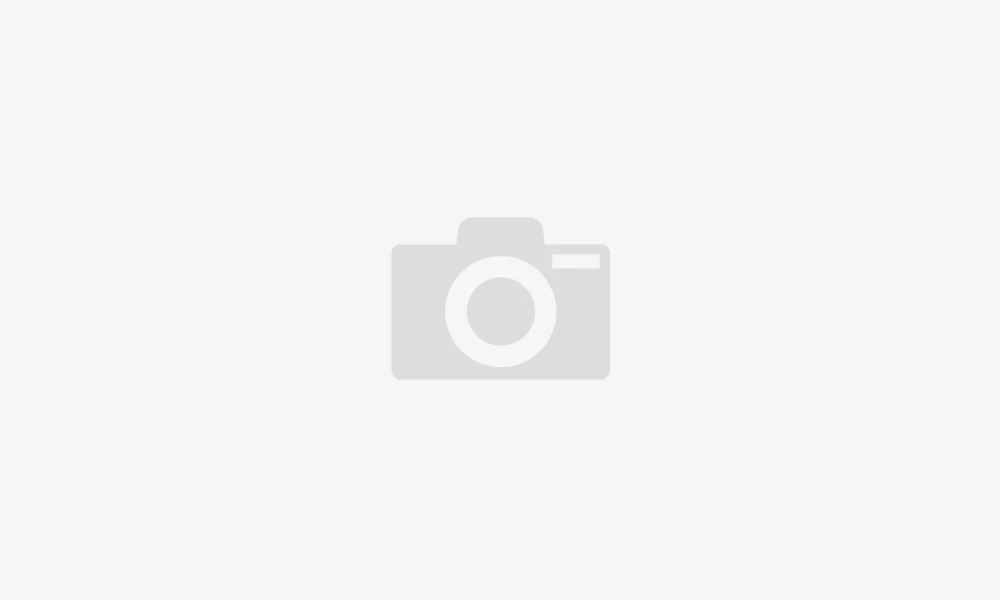
Nipa Commercial Corporation
From Navi Mumbai, Maharashtra, India, 400705
Nipa Commercial Corporation is suppliers from Navi Mumbai. It is established in year 1969 and having 300 plus employees.The contact address of Nipa Commercial Corporation is Plot No. 105/24, Sector No. 23, Janata Market.
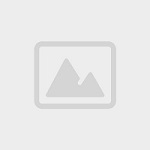
Petece Enviro Engineers
From Coimbatore, Tamil Nadu, India, 641018
Petece Enviro Engineers is suppliers from Coimbatore. It is established in year 2008 and having 200 plus employees.The contact address of Petece Enviro Engineers is No. 1, Head Quarters Road, Uppilipalayam.
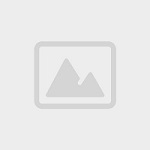
DPL Valves & Systems Private Limited
From Mumbai, Maharashtra, India, 400064
DPL Valves & Systems Private Limited is suppliers from Mumbai. It is established in year 2002 and having 200 plus employees.The contact address of DPL Valves & Systems Private Limited is Unit No. 124, Raj Ratna Industrial Estate B. J. Patel Road, Off Marve Road.
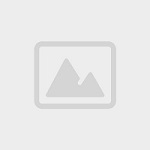
Leelam Industries
From Ahmedabad, Gujarat, India, 382430
Leelam Industries is suppliers from Ahmedabad. It is established in year 1986 and having 100 plus employees.The contact address of Leelam Industries is PLOT NO 348 ROAD NO 7,KATHWADA GIDC,.
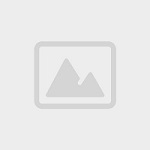
Unity Construction Equipment
From Ahmedabad, Gujarat, India, 382415
Unity Construction Equipment is suppliers from Ahmedabad. It is established in year 2008 and having 100 plus employees.The contact address of Unity Construction Equipment is shed no.21 Nilkanth avenue estate, viratnagar ring road crossing.
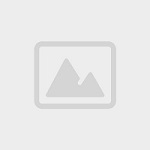
Lokpal Industries
From Greater Noida, Uttar Pradesh, India, 201301
Lokpal Industries is suppliers from Greater Noida. It is established in year and having plus employees.The contact address of Lokpal Industries is A-202 Defence Colony.
Frequently Asked Questions on Vacuum Pumps
1. What is Vacuum pump
vacuum pump is a device that removes gas molecules from a sealed volume in order to leave behind a partial vacuum.
2. What are the types of vacuum pumps
Different types of vacuum pumps
- can then be divided into Primary (Backing) Pumps
- Booster Pumps and secondary (High Vacuum) Pumps
- High, very high, and ultra-high vacuum pressure ranges
- There are two basic categories of vacuum pump
- Gas Transfer Pumps and entrapment or capture pumps
3. Which types of oil used for vacuum pumps
Maintaining clean oil in the pump ensures that the pump will operate at peak efficiency and prolong its life. vacuum pump acts as a blotter and absorbs all of the moisture and non-condensable. As the oil becomes saturated with these contaminants, the efficiency of the pump is dramatically reduced.
4. Vacuum pump used for
The vacuum pump mechanism is used to remove air or any gas particles from the container that creates a vacuum in the vessel. It is used for various industrial applications. It is used in electronics manufacturing units to produce CRT tubes, electric bulbs, and lamps, semiconducting materials, glass coating, etc.
5. What are some Advantages of Vacuum Pumps
They work on very slow rotational speed and augment the durability of the condition of the pumps
Vacuum Pumps are easy-to-use options as compared to other kinds of a pump its make less noise and vibrations these pumps are more efficient in handling condensable loadsThey come very handily in fabricating using any castable metal
6. What are some attribute of a vacuum pumps
Vacuum pumps are positive displacement compressors, which are equipped with single or double suction impellers, according to size. Fluid ring vacuum pumps do not need lubricants; there are no parts in direct contact inside the hydraulics.
7. What can a vacuum pump be used for
Vacuum pumps are used in an industrial setting to produce vacuum tubes and electric lamps, and to process semiconductors. They can also produce a vacuum that can then be used to power a piece of equipment.
8. What is the price of different types of the Vacuum pumps
Different types of Vacuum pumps price range such as -
Product Name | Price |
---|---|
Vacuum Pump SD-15-DS | Rs 8,000/ Piece |
Industrial Vacuum Pump | Rs 24,500/ Piece |
Vacuum Pressure Pump | Rs 5,500/ Piece |
Rotary Vacuum Pump | Rs 4,800/ Piece |
5-25 hp Jurop Vacuum Pump | Rs 50,000/ Piece |
Automatic Metal Vacuum Pumps | Rs 52,000/ Piece |
9. Can I use hydraulic oil in a vacuum pump
Hydraulic oils can also be used but will not pull the rated pump vacuum again due to the high vapor pressure.
10. How do you maintain a vacuum pump
Maintaining your vacuum pump after each use. after each use of your vacuum pump, wipe with a clean soft cloth to remove excess dirt and oil changing oil. changing the oil is very important, as oil is at all times a lubricant, a coolant, and a sealant for your vacuum pump when should I change the oil changing the oil on a vacuum pump
The performance of vacuum pump is measured through the parameter of its pumping speed. The pump speed is determined by the rate of the volume flow of a pump form its inlet. This is measured in volume per unit of time. The pumping rate depends on the type of vacuum pump being used and the gases being worked with. Thus, it means that the chemical composition of the gases will have a say in the average volume flow rate of the pump.
Another factor which influences the performance level of a vacuum pump is the throughput which means pumping speed multiplied by the gas pressure in the inlet. Therefore, a number of molecules pumped out of per unit time at a constant temperature is known as throughput.
Vacuum Pump operates by removing the air from the enclosed system by suction. This is done to decrease the air density of the enclosed space so as to create a vacuum. When the vacuum pump draws out all the air from the confined system, the mechanical input energy of a rotating shaft is converted into pneumatic energy.
As a result, the internal pressure level in a sealed volume becomes lower than that of the outside atmosphere. This pressure difference between internal and external atmosphere determines the amount of energy produced. The energy produced also depends on the volume of gas or air removed.
Types of Vacuum Pumps
There are different types of vacuum pumps which run on a common function based on the scientific principle to remove air, gases, and vapor from a confined space to create a vacuum in that space.
But basically, there are three different types of vacuum pumps:
1. Positive Displacement Vacuum Pumps
Positive displacements vacuum pumps find application where there is a need to create low vacuums. The primary use of such pumps is to enlarge a cavity so that gases can eject out of a sealed atmosphere.
The examples of such pumps are liquid ring vacuum pumps and roots blower which find extensive application in the industries where it is imperative to create a vacuum in a constricted space.
After this, the cavity is again sealed and exhausts the chamber. The rudiments of the principle on which positive displacement vacuum tubes work entail creating a vacuum by expanding the volume of the container.
For instance, in manual water pumps, a small sealed cavity or chamber is expanded and a deep vacuum is created. This leads to a pressure difference and some fluid from the chamber is drawn by the pump’s small cavity.
Once the fluid is pushed into the cavity it is sealed from the chamber and opened to the atmosphere and again shrunk to its smaller size.
Another case in point regarding the positive displacement vacuum pump is found inside our very body- diaphragm muscle. This muscle expands the chest cavity and increases the volume of the lungs.
These expanded lungs cause a partial vacuum and reduce the pressure. filled by air pushed in by atmospheric pressure.
2. Momentum Transfer Vacuum Pumps
As conjectured by the name, in momentum transfer vacuum pumps, the gas molecules accelerate from the vacuum side to rush towards the exhaust side. The pump’s function is based on the scientific principles of fluid dynamics which explain that matter flows differently at different pressures.
To understand momentum transfer vacuum pumps, one must know about viscous flow. The gas molecules under atmospheric pressure and mild volumes are in constant interaction and push each other. This is called viscous flow.
These molecules also strike against the walls of the chamber or container. Therefore, when the distance between molecules increases, the interaction between the molecules and walls also increases. This stage of high vacuum is said to be more effective than positive displacement pumps.
The momentum transfer vacuum pumps are further categorized into two types of vacuum pumps – diffusion pump and a turbomolecular pump. Both these pumps shove gas molecules to get diffused into the pump.
The major difference between these two pumps is that turbomolecular pumps use high-speed fans to blow out the gas molecules and diffusion pumps make of jets of oil to effectuate the purpose.
3. Entrapment Pumps
Entrapment pumps exploit chemical and therefore are more than efficient on performing the work as they are placed inside the chamber. The molecules in the air create a thin film.
This film is removed by the chemical reaction with the internal surface of the pump which is triggered by the entrapment pumps. Such vacuum pumps use cold temperatures to condense gases to a solid state.
To create ultra-high vacuum chambers, the entrapment pumps are used along with positive displacement vacuum pumps and momentum transfer vacuum pumps.
The aforementioned pumps are further classified into chemical process pumps, liquid ring vacuum, single cone vacuum pumps, close couple vacuum pumps, two stage vacuum pumps, and twin lobe roots blower.
What are the main components of Vacuum Pumps
There are many people who intend to use vacuum pumps for unconventional purposes and might not have an understanding of the parts of the vacuum system. Before you take to using this system, you must have basic knowledge about the functions of the major components of the vacuum pump.
Below are the prominent parts of the vacuum system and with their functions:
- Vacuum suction cups or Special grippers: These provide the interface between the vacuum system and the work piece.
- Mounting elements: They ensure quick and flexible connection of the vacuum components with the tooling system.
- Vacuum generators: They create a centralized or decentralized vacuum generation by using ejectors, pumps or blowers.
- Switches and system monitoring: They belong to the measuring and control components which ensure the safety of the users.
- Filters and connectors: The main function of filters is to protect the vacuum generator; hoses and connectors connect the components.
- Valves: Valves are used to control the vacuum as well as the compressed air.
What are the applications of Vacuum Pump
Vacuum Pumps have great utility in numerous industrial and scientific applications. They are used extensively in many industries like chemicals, cement, pulp & paper, sugar mills, treatment plants, process industries & power plants, pharmaceuticals, etc.
Below mentioned are some of the industrial uses:
Advantages and Disadvantages of Vacuum Pumps
- Composite molding
- Automobile industry
- Medical applications which require suction like radiotherapy, radiosurgery and radiopharmacy
- Flight instruments,
- Production of vacuum tubes and electric lamps
- CRT’s
- Semiconductor processing such as ion implantation, dry etching, and in the deposition of PVD, ALD, CVD, and PECVD
- Analytical instrumentation which analyzes solid, gas, surface, liquid and biomaterials
- Electron microscopy
- Photolithography
- Uranium enrichment
- Print presses
- Trash compacting
- Glass and stone cutting factories
- Cabinetry fabrication
- Ophthalmic coating
- Sewage systems
- Vacuum coating and engineering are required for decoration, durability etc.
- Glass coating
- Dairy equipment such as milking machines
- Air conditioning service
Advantages:
- Vacuum Pumps are easy-to-use options as compared to other kinds of pumps
- They make less noise and vibrations
- These pumps are more efficient in handling condensable loads
- They work on very slow rotational speed and augment the durability of the condition of the pumps
- They come very handily in fabricating using any castable metal
- They require less maintenance and re-building them is very easy
- It dispenses with the need of doing internal lubrication as metal-to-metal contact is not there in the compression chamber.
Disadvantages:
- These pumps may lead to cavitations
- Their motors are in large in size
- Efficiency and vacuum degree is a bit low
Explore By Cities
- Vacuum Pumps in Chennai
- Vacuum Pumps in Ahmedabad
- Vacuum Pumps in Pune
- Vacuum Pumps in Mumbai
- Vacuum Pumps in Delhi
- Vacuum Pumps in Thane
- Vacuum Pumps in Hyderabad
- Vacuum Pumps in Nagothane
- Vacuum Pumps in Kanpur
- Vacuum Pumps in Surat
- Vacuum Pumps in Faridabad
- Vacuum Pumps in Coimbatore
- Vacuum Pumps in Mandi Gobindgarh
- Vacuum Pumps in Bengaluru
- Vacuum Pumps in Ghaziabad
- Vacuum Pumps in New Delhi
- Vacuum Pumps in Vadodara
- Vacuum Pumps in Navi Mumbai
- Vacuum Pumps in Ambala
- Vacuum Pumps in Kolkata
- Vacuum Pumps in Vijayawada
- Vacuum Pumps in Ernakulam
- Vacuum Pumps in Visakhapatnam
- Vacuum Pumps in Panipat
- Vacuum Pumps in Mysore